矿渣粉磨球磨关键,矿渣粉磨生产工艺
概述: 由于钢渣韧性大,易碎性差,并且含有一定的金属铁粒,既难破又难磨,粉磨效率低,电耗高,粉磨成本高,如何提高粉磨效率,降低... 免费询价!
矿渣粉磨球磨关键,矿渣粉磨生产工艺尽在上海矿山破碎机网, 上海矿山破碎机网提供沙石厂粉碎设备、石料生产线、矿石破碎线、制砂生产线、磨粉生产线、建筑垃圾回收等多项破碎筛分一条龙服务。
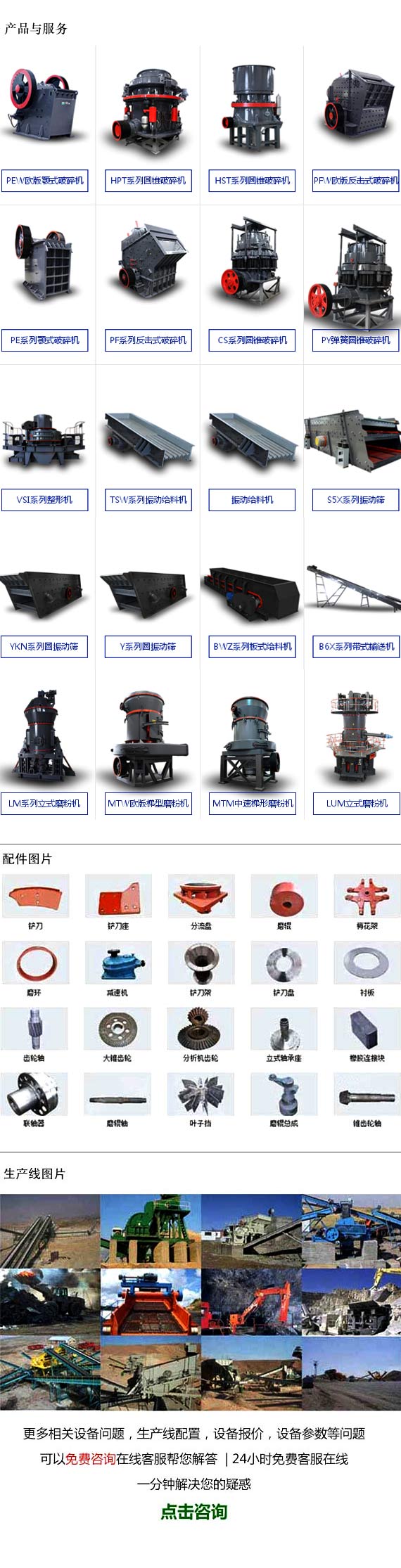
由于钢渣韧性大,易碎性差,并且含有一定的金属铁粒,既难破又难磨,粉磨效率低,电耗高,粉磨成本高,如何提高粉磨效率,降低粉磨电耗,直接影响到钢渣资源的综合利用水平。钢渣比矿渣易磨性更差通过钢渣和矿渣进行易磨性试验对比,结果发现钢渣与矿渣的易磨性均较差,但两者表现出不同的特点。
对钢渣进行邦德功指数(Wi)测试为Wi=kWh/t,高于普通熟料的平均值约%,可见,钢渣的易磨性很差,磨机产量必然低。钢渣含铁粒较多钢渣是钢铁厂炼钢时排出的废渣,在钢厂的排渣过程中,必定会排出一些金属铁,这部分铁虽经多次破碎分选回收,但不可能完全分选干净。钢渣在粉磨过程中,包裹于钢渣中的铁粒被逐渐剥离,形成金属颗粒聚集在磨内,严重地影响磨机的粉磨效率,增加衬板和研磨体的消耗,使粉磨状况恶化,而导致磨机低产高耗。
钢渣磨蚀性更强钢渣和矿渣都属于脆性材料,但相对而言,钢渣不仅硬度高,而且韧性也大,这造成了钢渣的磨蚀性大,易磨性差。
矿渣粉磨工艺
如普通水泥磨中,隔仓板盲板的使用寿命可达两年左右,而在粉磨钢渣水泥的磨机中,盲板使用不足一年便已磨坏。
一般Φmm开流钢渣磨,在钢渣细度为R=%~%,比表面积为~00m/kg时,磨机产量仅为~t/h,较其矿渣粉磨球磨关键,矿渣粉磨生产工艺普通水泥磨产量低0%~%。
由长沙深湘通用机器有限公司研制的柱磨机做预粉磨成功的解决了这一难题,并且已经在实际应用中取得了较好的效果。
柱磨机与辊压机相比,其挤压料层的形成是靠下部储料装置完成,因而很好的解决了物料进料细流动性好硬度高而难以进一步粉磨的矛盾。磨机细碎钢渣的性能特点:适应性强,特别矿渣粉磨球磨关键,矿渣粉磨生产工艺适用各种难碎难磨物料,且破碎比大,生产效率高能耗低,吨物料电耗仅-Kwh;破碎产品粒度小,-mm达%左右;易损件采用高合金材料制成,耐磨性好,以ZMJA为例,一套易损件可连续破碎钢渣近0万吨(吨钢耗小于0.元);由于该机属于料层粉碎,对于钢渣中一般的钢块能顺利排出,其安全装置则可对大块杂钢予以排除;设备占地面积小,安装简便,噪音低,扬尘少;设备运行稳定,故障率极低,维护简单。
应用实例:河北承钢年使用一台ZMJ柱磨机破碎难磨含钒钢渣,其工艺为:鄂破→柱磨机→台ф1.86.5m球磨机,柱磨机进料粒径为mm,出磨粒径为mm,产量≥t/h,系统生产能力提高5%,电耗下降%(柱磨机出磨粒径可在-mm间自由调节)。关键词:料床粉磨立磨辊压机筒辊磨导言自年磨机问世以来,已被广泛用于水泥及其矿渣粉磨球磨关键,矿渣粉磨生产工艺行业的物料粉磨,在目前仍占有主导地位。
传统的水泥及矿渣微粉制备多采用管磨机粉磨工艺,由于其粉磨空间开放四周不限,无法形成稳定的料床,故粉磨效率低单位粉磨电耗高粉磨成本高。随着科学技术的快速进步,以粉磨时间短粒度均匀的“料床粉磨”技术为代表的高效低能耗粉磨工艺及设备已成为当今水泥工业粉磨技术发展的主流。
生产矿渣粉
辊压机立磨筒辊磨等高效率料床粉磨设备,正在逐步取代传统的管磨机,用于水泥生产线中的生料煤粉制备及水泥矿渣微粉的终粉磨,并获得了良好的技术经济效果。不同粉磨工艺及其特点比较如前所述,以管磨机为代表的传统粉磨工艺,已有一百多年历史,粉磨过程将电能转化为机械能的同时,产生的声和热,消耗了大量电能,导致单位产品电耗居高不下,尤其是当入磨物料粒度大易磨性差或水份大时,磨机粉磨效率显著降低,更加剧了这一恶性循环。表管磨机与立磨辊压机筒辊磨粉磨特性对比指联合粉磨系统电耗;辊压机终粉磨电耗在2~Kwh/t;从表中数据分析认为:采用料床粉磨设备终粉磨水泥(或矿渣)时,其电耗基本相当,但比管磨机系统节电约%以上,除辊压机工艺系统较为复杂外,立磨与筒辊磨工艺系统比管磨机系统更简单些。从目前国内新建的新型干法水泥生产线来看,大多数生料制备系统采用立磨工艺,单位粉磨电耗kwh/t;同时,立磨自身集烘干破碎粉磨选粉收集输送功能于一体占地面积小粉磨效率高电耗低且运行稳定而成为机型。辊压机用于生料终粉磨,单位电耗低于立磨,因系统复杂程度及技术含量高,维护管理工作量大,国内采用的厂家极少。采用料床粉磨工艺终粉磨产品性能当前而言,立磨辊压机筒辊磨三种料床粉磨设备都可以用于水泥及矿渣微粉的终粉磨。
料床粉磨技术发展过程中,尤其在水泥终粉磨初期,曾经遇到磨细后的水泥成品,颗粒级配范围窄均匀性系数大标准稠度需水量大凝结时间过快等,立磨和辊压机的终粉磨均经历过此现象。筒辊磨问世较晚,在研发过程中鉴于前两种设备终粉磨出现的问题,在生产中加大了循环量,并通过调节其他工艺参数,较好地解决了这些问题。墨西哥某厂采用PolysuisRMC-/立磨配用SepolRMC高效选粉机磨制纯硅酸盐水泥,系统电耗Kwh/t,比闭路磨系统节电%以上,水泥质量良好。表水泥性能检测结果FLS公司引进小野田和神户制钢联合开发并改进的OK立磨广泛用于粉磨水泥及矿渣微粉,其磨辊呈曲面,带曲面凹槽的磨盘及磨辊在粉磨过程中可及时排出料床中的压缩空气,稳定料床及减少磨振。
表台湾某厂OK-立磨生产的水泥性能表中数据说明:在凝结时间标准稠度需水量基本相同的前提下,OK磨磨制的水泥d抗压强度比球磨水泥高出%,同时,水泥的早期强度也高,可进一步增加混合材掺量,降低水泥生产成本。
OK磨工作时,可通过调节磨盘转速辊压选粉机转速气流速度及磨内挡料圈高度等工艺技术参数达到调节水泥颗粒级配的目的,操作非常方便。采用OK磨制备比表面积~m/kg矿渣微粉时,与管磨机系统相比,OK磨粉磨电耗降低~%,节能潜力巨大,生产成本显著下降。
国内某公司采用进口立磨粉磨新型干法窑熟料制备不同强度等级的水泥,其实物质量数据见表:表立磨生产的水泥质量检测结果表数据进一步证实了国内现阶段采用立磨终粉磨,已解决了水泥标准稠度需水量过大颗粒级配范围窄(均匀性系数n值偏大)等相关技术问题。关于矿渣微粉粉磨工艺随着高性能混凝土技术的发展与应用,矿渣微粉已成为混凝土制备中不可或缺的第六组分材料(人工矿物掺合料)。粒化高炉矿渣系冶炼生铁时排出的工业废渣,每生产一吨生铁,大约排出~kg矿渣,其矿物成份在Cao-Sio-Alo三元相图中处于CASCASCSCS结晶区,大致化学成份为CaO4~%SiO~%AlO5~MgO~1%,并含有少量FeOMnOS及TiO和金属铁。矿渣出炉时经水淬急冷,保留了微晶态的高活性玻璃体结构,其有较高的潜在物理化学活性,在含有硫碱成份的水化环境中可激发出良好的水硬活性(如前苏联研究的碱-矿渣高强水泥属此类),可将矿渣看作是一种经过高温煅烧的高硅低钙熟料。
矿渣采用机械力活化,磨细制得的微米级粉体,具有潜在水硬性矿物的晶格产生畸变,发挥出优良的水化胶凝活性。
磨细矿渣微粉掺入水泥中的强度试验结果见表表磨细矿渣微粉掺入水泥中的胶砂强度由表数据可以看出:在含有矿渣配比%的矿渣水泥中掺入磨细矿渣微粉取代等量水泥后,水泥的早后期强度非但没有降低,反而有显著的提高,充分说明磨细矿渣微粉具有优良的潜在水硬活性,在水泥生产过程中对改善产品的物理力学性能具有重要意义。近年来,磨细矿渣微粉作为高活性矿物掺合料,已广泛应用于高性能高强混凝土,并对其技术机理的研究逐步微观化系统化深入化。不同比表面积磨细矿渣微粉应用于混凝土中的试验数据见表表不同比表面积矿渣粉砼的物理性能由表可知:在水泥用量基本相同的混凝土中,当矿渣微粉的掺入量也基本相同时,混凝土的强度随矿渣微粉比表面积的提高而提高。掺有磨细矿渣微粉的水泥及混凝土具有优良的抗渗性能和抗硫酸盐侵蚀性能,后期增进率高,大幅度提高了水泥石及混凝土的致密程度,尤其矿渣粉磨球磨关键,矿渣粉磨生产工艺适用于潮湿环境中及大体积水工混凝土的制备。国外,在海工混凝土配制过程中大量掺用磨细矿渣微粉,可以显著提高混凝土抵抗有害化学离子侵蚀能力及混凝土的耐久性与使用寿命。
当磨细矿渣微粉取代等量水泥掺入混凝土后,混凝土水化体系放热明显减少,内外部温差进一步缩小,降低了混凝土产生开裂的机率。
同时,由于整个水化体系中碱含量降低,为有效防止混凝土碱-骨料反应(AAR)的发生创造了良好的先决条件。采用管磨机粉磨工艺制备的比表面积≥m/kg矿渣微粉时,不仅单位粉磨电耗kWh/t,而且研磨体消耗量大,以中铬合金材质研磨体为例,吨矿渣粉的球锻磨耗50-g/t,如采用φ3.13m开流管磨机,磨机主电机功率为kW,生产比表面积≥m/kg矿渣微粉,台时产量也只有8t/h左右,单位粉磨电耗达7kWh/t,生产成本明显高于立磨。据了解,这些立磨生产线的单机产量一般都在t/h以上,矿渣微粉比表面积≥m/kg,单位粉磨电耗kWh/t,甚至kWh/t,而且磨耗也远低于管磨机系统,节电幅度%。挤压联合粉磨和筒辊磨系统在辊压及问世之初,主要用于预粉磨流程,其功效尚不能完全发挥,加之辊压机自身存在一定的技术缺陷:辊面磨损过快液压系统泄漏边缘效应等,经过二十余年的发展改进以及新材料新技术的应用,辊压机的技术性能不断得到完善,现阶段辊压机辊面工作寿命可达h以上,其他方面的问题也迎刃而解。但存在水泥颗粒级配范围过窄均匀性系数n值偏大水泥凝结时间过快(石膏分布不均匀缓凝效果差所致)成品颗粒形貌为多角形结构,导致水泥标准稠度需水量过大等。采用挤压联合粉磨工艺,主要是充分发挥辊压机的预粉磨功能,必须使辊压机多做功,才能增加挤压料中细粉的含量,辊压机多做功kwh,后续管磨机可节省-kwh,管磨机能够真正发挥其特有的研磨功能,在使系统获得高产低耗的同时,对入磨粗粉水泥的多角形结构颗粒进行“整形”,改善水泥的颗粒级配,降低需水性,以确保提高水泥的使用性能。采用挤压联合粉磨工艺可在原粉磨系统基础上增产~1%,单位粉磨电耗较普通管磨机粉磨工艺可节省%以上。
挤压联合粉磨系统的后续管磨机有开流和圈流两种形式,同一企业采用挤压联合粉磨工艺,后续均为φm管磨机,开流圈流两种不同系统制备的水泥性能见表:表挤压联合粉磨系统水泥质量检测结果从表得知,在相同熟料配比条件下,采用挤压联合粉磨工艺后续管磨机为开流系统时,所磨制的强度等级PO525水泥早后期强度略高于圈流系统粉磨的水泥。同时,凝结时间也要短些,水泥颗粒级配范围更宽些,开流系统单位粉磨电耗为Kwh/t,圈流系统单位粉磨电耗为Kwh/t。
国内牡丹江水泥公司年引进法国FCB公司研制的HoRomill筒辊磨用于粉磨水泥(国内台应用),装机功率kw,配用TSV选粉机,设计能力t/h,辊筒工作转速r/min,单位粉磨电耗为kwh/t。筒辊磨生产的水泥与球磨磨制的水泥物理性能对比见表:表筒辊磨与球磨磨制的水泥性能对比表中数据可以看出:相同混合材配比条件下,与球磨水泥相比,筒辊磨磨制备的水泥有更高的早后期强度,与立磨磨制的水泥性能基本相似,说明仍能进一步提高混合材掺量,降低生产成本。在水泥物理性能方面,筒辊磨生产的水泥标准稠度需水量仍略大于球磨机磨制的水泥,这可能是筒辊磨水泥颗粒形貌大部分为扁针状,水化过程比球形颗粒更快的缘故。结束语传统的管磨机粉磨工艺,其粉磨空间四周不限,难以形成料床,故效率低单位粉磨电耗高研磨体消耗大生产成本高。目前应用广泛的挤压联合粉磨系统部分引入了料床粉磨工艺,属成熟的节能工艺技术,但工艺系统布局较为复杂,随着时间的推移,将会逐步向立磨终粉磨过渡。
立磨辊压机筒辊磨均为料床粉磨的高效节电设备,实现了无球化终粉磨,用于制备水泥和矿渣微粉,相对传统管磨机粉磨工艺而言,节电幅度达~%以上,更有利于节能减排,发展循环经济,功在当代,利在千秋。
立磨集烘干破碎粉磨选粉收集输送于一体,并已率先实现大型化,工艺流程简单占地面积小,单位粉磨电耗和金属磨耗低,是当前大中型水泥及矿渣微粉制备企业的高效粉磨工艺设备。立磨筒辊磨与传统管磨机粉磨工艺所制备的水泥力学性能相比,具有更高的早后期强度,可以增加混合材掺加量降低吨位水泥制造成本,综合提高经济效益。无论磨制水泥或矿渣微粉,要求磨前设置多道强力除铁,由于单质铁粒具有铁磁性和可塑性,难以磨细的同时在磨内产生富集,加剧设备磨损,必须予以除去。
热销产品
相关资讯
栏目
- 山东大理石叶岩振动筛 - 2017/10/26
- 海城市振动给料机 - 2017/10/24
- 黑龙江鹤岗轻质碳酸钙鄂式破碎设备 - 2017/10/21
- 瓷土加工腻子粉生产技术 - 2017/10/20
- 山东济宁页岩鄂式碎石机 - 2017/10/17
- 型碎石机 - 2017/10/14
- 圆锥破碎机买卖 - 2017/10/12
- 山东边角料采用新型干法生产水泥主要用哪些粉磨设备 - 2017/10/10
- 江西九江人造大理石鄂式碎石机 - 2017/10/08
- 杭州哪里有卖碎大理石的机器 - 2017/10/05
- 锤式破碎机故障与维修 - 2017/10/02
- 山西花岗岩加工立磨机试图 - 2017/10/01
资料下载
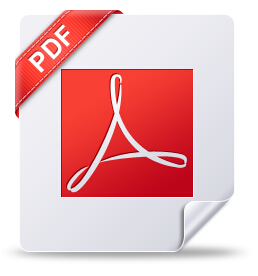