矿热炉生产工艺流程,矿热铜瓦生产设备
概述: 工业硅生产是高能耗行业,平均每吨工业硅需要消耗KWh电以上,全国年产万吨工业硅需要亿KWh以上。目前金属硅冶炼技术依旧... 免费询价!
矿热炉生产工艺流程,矿热铜瓦生产设备尽在上海矿山破碎机网, 上海矿山破碎机网提供沙石厂粉碎设备、石料生产线、矿石破碎线、制砂生产线、磨粉生产线、建筑垃圾回收等多项破碎筛分一条龙服务。
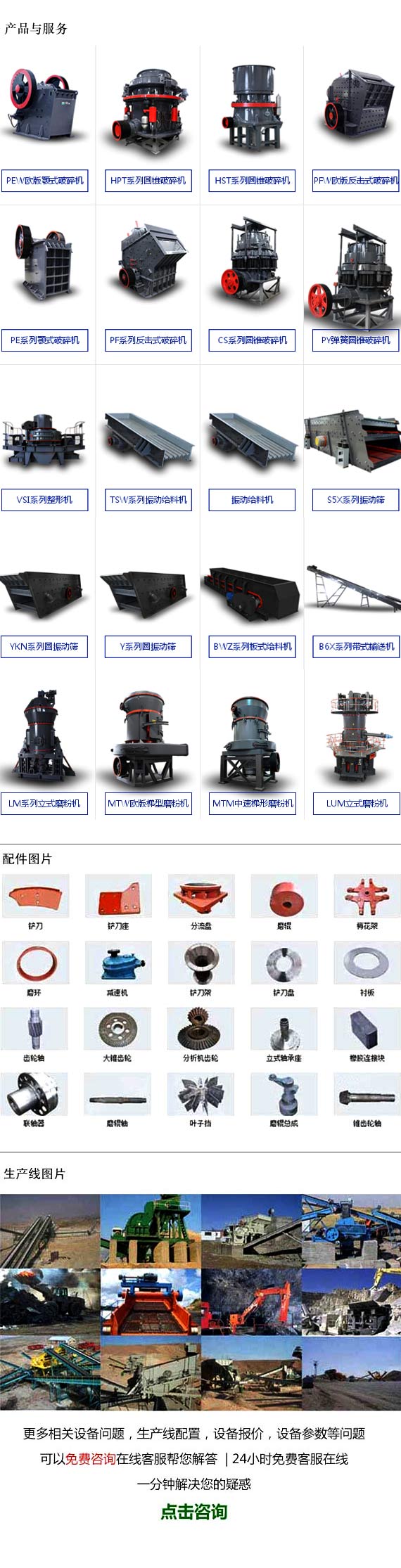
工业硅生产是高能耗行业,平均每吨工业硅需要消耗KWh电以上,全国年产万吨工业硅需要亿KWh以上。目前金属硅冶炼技术依旧存在较大问题,设计配置不合理,冶炼设备技术落后电耗过高效益差员工操作水平不均。大容量矿热炉具有单炉产量大能量供应均衡性好便于实现机械化便于降低能源消耗热稳定性好便于操作等一系列优点,是业界一致认可的矿热炉发展的方向。国内现有设计生产KVA工业硅矿热炉已达近百台,布置设计五花八门,炉型设计十分广泛,生产操作细节缺乏。研究金属硅冶炼生产核心技术的研发动向工艺设备技术应用及趋势对于企业提升产品技术规格,提高市场竞争力十分关键。综合多个项目研究,经过几年现场设计生产实践,本文仅对KVA工业硅矿热电炉选型设计及生产实践进行研究,供同行参考。一半密闭式KVA工业硅矿热炉的设计正确设计矿热炉的结构是保障矿热炉工作性能的先决条件,是设计工作者面临的困难。好的矿热炉结构设计不仅有利于炉子保障高产优质低能耗少故障的生产,而且有利于节约建设成本方便其矿热炉生产工艺流程,矿热铜瓦生产设备设备布置保证操作顺畅。高效节能先进工业硅冶炼技术工艺,是衡量一个企业是否具有先进性,是否具备市场竞争力,是否能不断领先于竞争者的重要指标依据。
设计上不合理体现在我国普遍使用的是KVA左右的小炉型(散热大产量低)炉型设计上为隔热措施不严密电路设计不合理极心圆尺寸大小不合理等许多细节方面。
矿热炉设备
一)工业硅矿热电炉特点:炉型大型化则单位热容率增大,能量供应集中,通过外围表面单位面积散热小炉子热稳定增强,有利于降低热损失,提高冶炼效率。
冶炼工业硅采用先进技术和设备,炉变选用低阻抗电压的恒功率电炉变压器,功率因素高,超负荷能力强;短网采用通水式铜管,电极三角全补偿式外短网,短网软缆采用水冷电缆,阻抗损失小;科学选用石墨电极;有利于高产降耗,电炉炉型采用矮烟罩半密闭式,有利于收尘,工人操作环境好;电极把持器的铜瓦采用液压波纹管压紧式;电极升降采用液压,捣炉机选用半液压式大功率捣炉机。
二)矿热电炉结构选型技术参数:在工业硅冶炼过程中矿热炉的状态与电气参数的变化密切相关,控制的供电制度对保证取得好的经济技术指标十分重要。图KVA电炉部分示意图炉壳部分:国内外对炉衬炉底散热强度计算表明,保持炉衬与炉底热损失为%~%是在合理的范围内,或者保持炉衬表面温度在~0℃是允许的,因此按照这个条件以及结合所选择材料的使用温度,根据传热学知识可确定炉衬与炉底工作层保温层隔热层绝热层的厚度,钢板层的厚度根据强度需要而定。炉壳过大,从而炉衬厚度过厚,引起筑炉成本上升,出炉困难,占地面积扩大,炉衬表面积增加,散热面积增大;炉壳过小,炉衬厚度过薄,抑或炉衬强度不够,抑或无法保温。
采用炉壳直径mm,高mm,两个出铁口,夹角,炉壳钢板厚mm,炉底厚mm,腰带及竖筋为0mm槽钢,炉底工字钢高为mm。设计中,工作层都使用高炉碳砖保温层选用新型隔热耐火粘土砖(热导率W/(mK)及高炉砖隔热层用粒度为~mm的细硅石与矿渣混合物绝热层使用石棉纤维板钢板层选用mm厚的普通钢(炉底钢板厚mm)。如图电极孔烟罩上盖板烟囱孔冷却水道观测孔捣料炉门红砖隔热耐火砖纳米绝热材料复合硅酸铝纤维毯钢板1出硅口1高铝砖1自焙炭砖图0KVA工业硅矿热炉结构图电极直径的选择:在确定矿热炉其矿热炉生产工艺流程,矿热铜瓦生产设备结构尺寸之前,必须先确定电极直径,矿热炉生产工艺流程,矿热铜瓦生产设备决定着矿热炉其矿热炉生产工艺流程,矿热铜瓦生产设备结构尺寸的大小。电极直径有许多计算方法,一般根据电极电流和电极电流密度确定:d=式中I为电极电流,A,△I为电极电流密度-A/cm。
炉膛深度内径确定:在选择炉膛深度时,要保证电极端部与炉底之间有一定的距离电极有效插入的深度和料层有一定的厚度。
生产矿热炉
炉膛深度若过深,电极与炉底距离远,电极不能深插,高温区上移,炉底温度低,炉底SiC会沉积,炉底上抬,堵塞出硅口,炉况变差。否则,炉膛内径选择尺寸过大,矿热炉表面散热面积大,矿热炉生产工艺流程,矿热铜瓦生产设备还原剂烧损严重,出硅口温度低,出硅困难,炉况会恶化。
炉膛内径选择过小,电极炉料炉壁回路上通过的电流增加,反应区偏向炉壁,将使炉内热量分散,炉心反应区温度低,炉壁腐蚀严重,炉况也会恶化。烟罩结构与材料选择:大容量矿热炉炉膛尺寸跨度大,烟罩设计较困难,同时从烟罩通过的电流大,处理不好涡流损失大。为了解决烟罩结构强度与防止涡流损失,采取用水冷钢管(防磁)做骨架并起吊,上下盖采用石板与水泥构筑,用细钢筋做支撑,既减轻了烟罩整体重量又防止了筑砌或制作上的不便。
炉门结构与材料选择:大容量炉的问题是炉缘距离炉心远,上料困难,特别是国内强调以人工精细加料来取得好质量与低能耗产品的观点下,普遍认为在大容量炉子在国内不如KVA炉子的性能,因此一次又一次的阻碍了投资方建造大容量炉子的热情。设计个炉门用于加料处理炉况和捣炉,三侧捣炉大炉门有效操作空间高度为mm,操作孔炉门为对开式。工业硅炉冶炼过程中,极心圆参数是重要的参数,在电极上下运动过程中,为防止电极摆动而折断电极和极心圆的变化,同时防止炉内烟气从上部逸出,因此在水冷大套设有密封导向装置。
电炉排烟系统:主烟道:根据冶炼过程中产生的烟气量及半密闭炉的野风量,设计烟管为两根直径00mm排烟管。由于烟气温度高,为改善设备的工矿条件,设计烟管底部约米高为双层水冷,材料采用Q,厚度为mm,其连接采用两道绝缘法兰连接,绝缘材料HP-。
矿热炉生产工艺
其余为单层,材质为Q,厚度mm,第三层平台上部留有除尘管道接口,接口上端为翻板碟阀,此碟阀为手动控制。电炉电极系统:极心圆直径是一个对冶炼过程有很大影响的设备结构参数,电极极心圆直径选得适当(图-),三根电极电弧作用区域部分刚好相交于炉心,各电极反应区既相互相连又重叠部分最小,在这种情况下,炉内热量分配合理,坩埚熔池,吃料均匀,炉况稳定,炉况也易于调节。
结合矿热炉容量可调极心圆范围,设计中极心圆直径可按下式计算:Dg=ad;式中a为极心圆倍数,a=-。图-极心圆适当图-极心圆过小图-极心圆过大图极心圆图示电极系统由电极电极把持器电极升降机构和电极压放装置组成。电极采用(电流密度~/Acm),把持器由导电铜瓦导电铜管压力环及电极极心圆调整机构等构件组成。电极升降设计:电极直径mm(石墨),包括上把持筒,下把持筒,水冷大套,油缸压力环,导电铜管夹持装置及吊挂装置等。
电极升降设计为液压升降,工作平稳,防止卷扬机升降造成工作不平稳,在冶炼过程中卷扬机不能有效对电极起把持作用,把持系统容易不垂直造成在炉膛内极心圆的变化,对冶炼造成影响。
矿热炉生产
油缸在第三层平台,为吊挂式结构,每根电极用两个缸径的升降油缸进行提升,提升高度米,提升速度m/min。铜瓦抱紧机构采用油缸式压力环夹紧铜瓦,由于每个油缸是独立工作,因此使每块铜瓦与电极能紧密接触,防止铜瓦与电极产生刺火现象而影响铜瓦寿命,电流传递稳定,接触电阻小,电能损失小。电极压放:电极压放为双液压抱闸之间三个压放油缸来执行,压放油缸直径15mm,行程mm,液压抱闸采用碟簧抱紧液压放松,闸瓦硫化橡胶,mm厚的绝缘橡胶。短网系统:短网的布置和布局结构紧凑投资小,便于加工,设备占地面积小设备投资较小维修简单,事故率低。水冷电缆具有良好的冷却效果,(许用电流密度约~A/mm),是管式短网(许用电流密度约~A/mm)的配套技术,锻造铜瓦(许用电流密度约2.~A/mm),锻造铜瓦于电极接触面(许用电流密度约2.~A/mm),具有质量轻投资省运行可靠结构紧凑与布置排列优化等优点。
电炉采用净循环水,水质要求为低硬度软水(~mg/L)(CaO)(~dH)悬浮物小于mg/L,进水温度应低于C,供水点的压力为MPa;进出水温差控制在C左右,循环水量为约1㎡/n高流速和大流量的要求。
出料系统:出硅口是矿热炉上非常重要的一个部位,矿热炉生产工艺流程,矿热铜瓦生产设备的位置结构形状尺寸材料选择都是需要仔细斟酌的。位置布置不当,出硅口部位温度低,出硅不畅或者是操作不方便;结构形状尺寸不当,也会导致出硅不畅或者封堵困难或者出硅时间延长;材料选择不当,容易氧化腐蚀,维修频繁。
设计中,出硅口设计二个,每个出硅口水平位置与炉底齐平并比炉底水平线下倾斜℃,角度位置矿热炉生产工艺流程,矿热铜瓦生产设备处于炉心与电极中心两点的延长线与炉壁的焦点上。基本组成:高压供电系统由高压进线隔离开关及电压互感器高压真空断路器及电流互感器氧化锌避雷器及阻容吸收保护装置组成。所用高压断路器为真空型,主要用来接通或断开主回路切断由于电弧短路而造成的过电流,同时矿热炉生产工艺流程,矿热铜瓦生产设备还可以用来为炉子设备提供短路保护。基本功能:在高压室设面高压柜,进线柜(隔离开关+电压互感器)真空开关氧化锌避雷器及阻容保护装置,然后用电缆联络至变压器室。高压供电系统可向炉子提供kV主电源,并可进行主回路短路保护,在高压回路设置双重过电压吸收装置,吸收操作过电压及浪涌电压,以保护变压器。二KVA工业硅矿热电炉生产实践电炉生产工业硅,炉况容易波动,较难控制,因此必须正确判断炉况并及时处理。
影响炉况的因素是很多的,但是在实际生产中,影响炉况最主要的因素矿热炉生产工艺流程,矿热铜瓦生产设备还是矿热炉生产工艺流程,矿热铜瓦生产设备还原剂用量,矿热炉生产工艺流程,矿热铜瓦生产设备还原剂用量不当会使炉况发生急剧变化。一般来说,炉况变化通常反应在电极插入深度电流稳定程度炉子表面冒火情况,出硅情况及产品质量波动情况等几方面。我国工业硅行业长期依靠廉价电力维持生存的年代一去不复反,企业要想获得较好的经济效益,必须提高操作技术水平。为了提高工业硅冶炼的高度和精度,需要特别注意控制冶炼过程中的各个环节:一)电炉高温冶炼在具体操作中必须千方百计地减少热损失,基本上保持或扩大坩埚。
热销产品
相关资讯
栏目
- 东北金矿石加工韶关市颚式碎石机生产厂家 - 2017/04/22
- 石灰的生产过程,石灰的粉磨功指数 - 2017/04/22
- 咸阳石英石沃破机,咸阳粉煤灰销售点 - 2017/04/22
- 怀仁哪里有煤矸石,怀化市石灰加工厂 - 2017/04/22
- 山西硅石加工粉磨冶金成套设备 - 2017/04/22
- 山西铜矿加工立式辊磨研磨技术 - 2017/04/22
- 鄂式碎石机250-1000的价格 - 2017/04/22
- 伊利石生产线工艺流程 - 2017/04/22
- 电厂炉底干渣磨细,电厂炉渣怎么粉磨 - 2017/04/21
- 动力粉砂机,动式破碎机,动态分离器 - 2017/04/21
- 直通离心磨粉机独居石 - 2017/04/21
- 山东边角料采用新乡市华鑫水泥厂 - 2017/04/21
资料下载
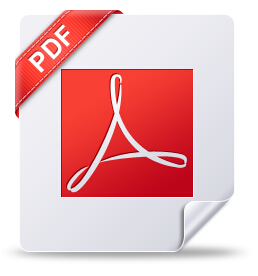