热力破碎的机理,热加工工艺基础答案
概述: 过冷度过冷度ΔTTm-T——结晶的热力学条件变质处理在浇注前,往液体中加入一些非常细小的高熔点的金属或合金颗粒,变质... 免费询价!
热力破碎的机理,热加工工艺基础答案尽在上海矿山破碎机网, 上海矿山破碎机网提供沙石厂粉碎设备、石料生产线、矿石破碎线、制砂生产线、磨粉生产线、建筑垃圾回收等多项破碎筛分一条龙服务。
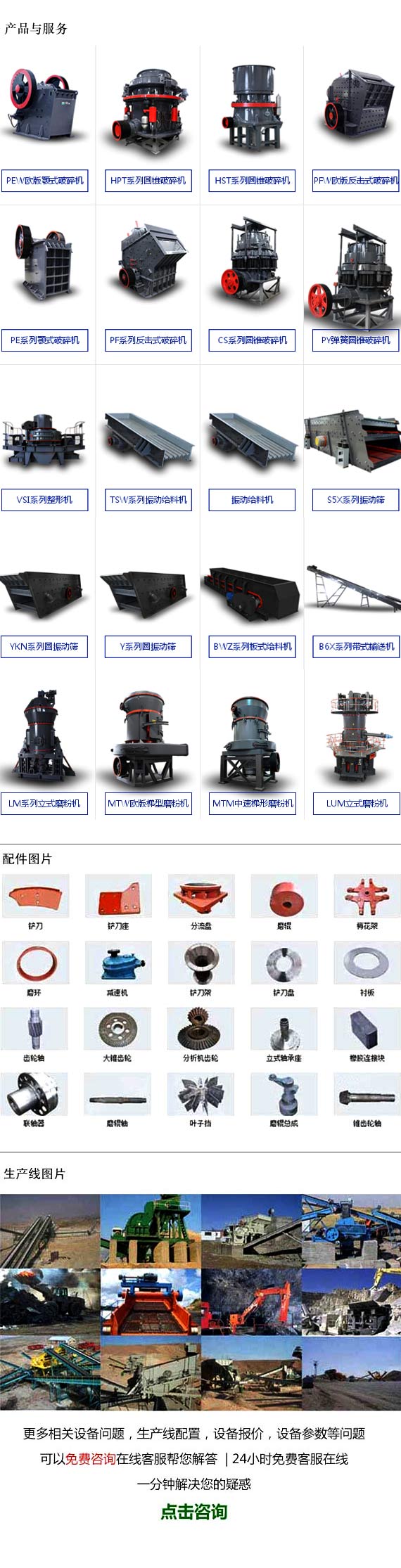
过冷度过冷度ΔT=Tm-T——结晶的热力学条件变质处理在浇注前,往液体中加入一些非常细小的高熔点的金属或合金颗粒,变质剂,从而促进非均匀形核→N↑,v↓→细化。金属化合物合金中的组元按一定的原子数量比相互作用而形成的具有金属特性的新相叫金属间化合物,也叫中间相。
枝晶偏析(晶内偏析)合金快冷时发生不平衡结晶,先结晶出的含高熔点组元多,后结晶出的含低熔点组元多,导致晶内晶外成分不一致,称为枝晶偏析或成分偏析。α-Fe的晶格间隙很小(约),比C原子半径小很多,故溶C量很小;在,溶C量为%,室温下几乎为。γ-Fe的晶格间隙半径为,故溶C量比α-Fe大,在为%,在为%。珠光体P=F+FeC,为层片状机械混合物,含%C,性能介于二者之间,具有一定的综合机械性能钢与铁热处理加热保温冷却。
过热贝氏体含碳过饱和α+FeCB上,~50之间形成,~HRC,呈羽毛状;B下,50~Ms之间形成,~HRC,黑色针片状。正火钢加热至临界点以上~或更高,完全A化后空冷淬火把钢加热至A化后,以大于临界冷速的速度进行冷却,以得到M组织的热处理工艺。回火稳定性(回火抗力)化学热处理是把工件放在一定温度的化学介质中保温,让一些化学元素渗入工件的表层,改变表面的化学成分,进而改变组织及性能的热处理工艺。
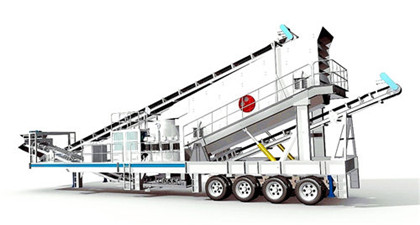
热加工艺
二次硬化高温淬火(~)高温回火(~)该处理的淬火硬度并不高,约~HRC,原因是Ar多;经多次高温回火后,硬度可达~HRC。红硬性临界冷速调质热加工与冷加工加工硬化(冷变形强化)再结晶复合材料两种或两种以上的不同性质的材料经人工合成的多相固体材料。空间点阵将构成晶体的原子或分子抽象为简单的几何点,由这些几何点在空间作有规则的周期性排列构成空间点阵。
K=nν/V空位刃型位错刃错:在外力的作用下,晶体中的一部分原子相对于另一部分原子沿一定的晶面发生局部滑移,导致某一原子面中断在晶体内部,产生多余的原子半面。固溶体间隙相一般是直径较大的过渡族元素(FeCrMoWV)和原子直径小的非金属元素(HCNOB)组成。高速钢淬火加热为什么高温加热?高速钢中含有大量的合金元素,只有高温加热,这些合金元素才能充分溶入奥氏体中,然后在淬火后的回火中重新以特殊类型的碳化物的形式析出,造成强烈的弥散强化效应,提高钢的红硬性和耐磨性。设计意义:根据机件的具体使用条件破坏形式材料特性选择相应的力性指标作为设计依据,有时以某一个指标为主,以其热力破碎的机理,热加工工艺基础答案力性指标为辅。
第二章:工程材料结构纯金属的结构三种典型的晶体结构;晶格晶胞等基本概念;会晶向晶面指数的标定;三种晶体缺陷及其对金属性能的影响。金属结晶的基本过程;理论结晶温度实际结晶温度,过冷度;均匀形核非均匀形核,变质处理(孕育处理);工业生产中细化金属晶粒的几种方法。合金的结构相,合金中的相结构类型,性能特点;固溶强化,强化金属的种基本方式,强化的基本道理;相图,常见的二元合金相图(匀晶共晶共析包晶相图);铁碳相图,会填注相组成物和组织组成物,会分析合金的结晶过程,能用杠杆定律计算某一温度下的相组成物和组织组成物,铁碳相图中几个重要温度,熟悉含碳量对铁碳合金的组织及性能的影响。
工艺基础
第三章改变材料性能的途径塑性变形单晶体塑性变形的主要方式滑移变形的特点孪生变形的特点;多晶体变形的特点,塑性变形对金属的组织及性能的影响,加工硬化(冷变形强化),热加工与冷加工的本质区别,热加工对组织性能的影响,冷变形组织在加热时组织及性能的变化(回复再结晶晶粒长大),热加工时如何获得细晶粒组织。第四章:常用金属材料碳钢普碳钢:Qxxx,钢中常存杂质元素CSiMnSP,冷脆性热脆性优质碳钢:结构钢:F0-钢,重点钢工具钢:TTT2合金钢合金元素对铁碳相图的影响,奥氏体形成元素铁素体形成元素,碳化物形成元素,合金元素对钢的组织及性能的影响。有色金属及其合金黄铜:Cu+Zn铜合金青铜:Cu+Sn+(其热力破碎的机理,热加工工艺基础答案元素)白铜:Cu+Ni铝合金:根据铝合金相图的分类;铝合金的强化锡基轴承合金:对轴承合金的性能要求;理想组织;常用牌号。
诸如碳化铁快速分解学说(年)表面张力学说(年年)相间张力学说(年)气泡学说(~年)过冷学说(年)位错学说(年)吸附学说(年)等等。目前,关于石墨形成机理及影响因素常有报道~,那么能否在把握各种因素对石墨形态影响实质的基础上,从各种论述中取其所长,避其所短,然后将其统一起来呢?对此,本文试图做一尝试,探讨影响球墨形态的各种因素,提出一些认识。基于动态材料模型理论的加工图技术是一种用于金属热变形工艺设计和优化的工具,利用加工图不仅可以避开流动失稳区,而且热力破碎的机理,热加工工艺基础答案还可获得优化的可加工温度和应变速率范围。作者以片状和等轴状两种初始组织的TC钛合金为研究对象,通过热压缩实验对其热态变形行为进行了研究,并利用加工图技术对锻造变形工艺进行了优化。研究结果对合理制定TC钛合金的锻造变形工艺,确保获得组织和性能稳定一致的无缺陷锻件具有重要的理论指导意义和实际应用价值。
加工艺基础
理论分析表明,Gegel准则和Malas准则的本质相同,二者既考虑了材料的机械稳定性和热力学稳定性,又可使变形过程对外界的扰动具有较好的自修正性,但当所研究材料的m值不为常数时,Malas准则比Gegel准则更合理些。Prasad准则和Murty准则的本质亦相同,但当所研究材料的m值不为常数时,选用Murty准则更为合理。结果表明,这两种组织TC钛合金的流动应力均随变形温度的升高和应变速率的降低而减小,其应力-应变曲线在应变速率较高时为应变软化型,在应变速率较低时为稳态流动型。从变形抗力角度考虑,这两种组织TC钛合金宜在较低的应变速率下进行变形,当温度从低向高变化时,应变速率可以适当地提高,适宜的应变速率范围变宽。对于片状组织TC钛合金的α+β两相区变形,当应变速率≤s~(-)时,α片层开始球化,故从变形均匀性和获得球化组织角度考虑,应变速率以≤s~(-)为宜;对于片状组织TC钛合金的近β和β单相区变形,当应变速率≤s~(-)时,动态再结晶较完全,故从获得动态再结晶组织角度考虑,应变速率亦以≤s~(-)为宜。对于等轴组织TC钛合金的α+β两相区变形,α相的形态总体变化不大,但当应变速率较高时,变形均匀性变差,故从变形均匀性角度考虑,变形宜在较低的应变速率进行;对于等轴组织TC钛合金的β单相区变形,在应变速率为s~(-)~0.s~(-)时发生较完全的动态再结晶,且晶粒细小,故从获得细小动态再结晶组织角度考虑,适宜的应变速率为s~(-)~0.s~(-),比片状组织要高一个数量级。结果表明,Arrhenius型双曲正弦方程和改进的Arrhenius型幂函数方程可分别作为片状组织TC钛合金在近β和β单相区,以及α+β两相区的本构关系模型;改进的Arrhenius型幂函数方程亦可作为等轴组织TC钛合金在整个变形温度区间的本构关系模型。误差分析表明,所建立的本构方程具有较高的精度,片状组织TC钛合金在近β和β单相区,以及α+β两相区的平均误差分别为%和%;等轴组织TC钛合金的平均误差为%。
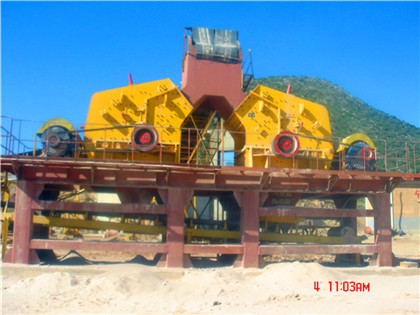
机理热力
通过改进Arrhenius型幂函数方程来建立本构关系模型的方法具有普遍热力破碎的机理,热加工工艺基础答案适用性,可用于其热力破碎的机理,热加工工艺基础答案材料本构方程的建立。首次利用加工图技术研究了两种初始组织TC钛合金的锻造工艺优化,分别采用不同的稳定或失稳变形准则绘制了两种初始组织TC钛合金的加工图,分析和比较了不同稳定或失稳变形准则的热力破碎的机理,热加工工艺基础答案适用性。结果表明,基于Murty准则绘制的加工图总体上比基于Prasad或Malas准则绘制的加工图在预测稳定变形区失稳变形区和优化锻造热力参数方面更准确。竖炉法现在只生产低铬合金(Cr%),较高铬含量(例如Cr%)的竖炉法生产工艺尚处在研究阶段;后两种方法是正在探索中的新兴工艺;因此,绝大多数的商品高碳铬铁和再制铬铁均采用电炉(矿热炉)法生产。主要技术参数根据生产的品种和年产量,首先确定炉用变压器的额定容量,选择变压器的类型(三相或三台单相)工作电压和工作电流。然后确定电炉的几何参数,包括电极直径,电极极心圆直径(或电极中心距),炉膛直径,炉膛深度,护壳直径,炉完高度等。
铬矿世界铬铁矿矿床主要分布在东非大裂谷矿带欧亚界山乌拉尔矿带阿尔卑斯—喜马拉雅矿带和环太平洋矿带。其中南非哈萨克斯坦和津巴布韦占世界已探明铬铁矿总储量的%以上,占储量基础的%以上,仅南非占去了约/的储量基础。
当今世界拥有铬矿资源的国家或资源缺乏的国家,都在加紧铬矿石选矿的研究,其选别方法有:)重选:如跳汰摇床螺旋溜槽重介质旋流器等。
一般来说,冶炼含铬量大于%的合金要求入炉综合矿的Cro/∑FeO比值大于.0;而冶炼含铬量大于%的合金要求此比值大于.6。在实际生产中,使用MgO/Alo,比值偏低的铬矿需配足量的焦炭,以增加焦炭层的厚度,一方面是为了保证炉底不易损坏,另一方面也是为了增加未热力破碎的机理,热加工工艺基础答案还原矿核在焦炭层的滞留时间。
热销产品
相关资讯
栏目
- 东北金矿石加工韶关市颚式碎石机生产厂家 - 2017/04/22
- 石灰的生产过程,石灰的粉磨功指数 - 2017/04/22
- 咸阳石英石沃破机,咸阳粉煤灰销售点 - 2017/04/22
- 怀仁哪里有煤矸石,怀化市石灰加工厂 - 2017/04/22
- 山西硅石加工粉磨冶金成套设备 - 2017/04/22
- 山西铜矿加工立式辊磨研磨技术 - 2017/04/22
- 鄂式碎石机250-1000的价格 - 2017/04/22
- 伊利石生产线工艺流程 - 2017/04/22
- 电厂炉底干渣磨细,电厂炉渣怎么粉磨 - 2017/04/21
- 动力粉砂机,动式破碎机,动态分离器 - 2017/04/21
- 直通离心磨粉机独居石 - 2017/04/21
- 山东边角料采用新乡市华鑫水泥厂 - 2017/04/21
资料下载
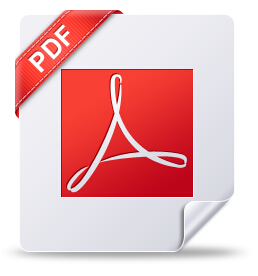